某石油化工企业废水处理絮凝剂应用案例分析
一、企业废水概况
该石油化工企业主要从事原油加工与化工产品生产,其废水来源广泛,包括原油脱盐脱水、油品精制、化工装置生产等环节。废水成分复杂,含有大量的石油类物质(如乳化油、浮油)、悬浮物(如泥沙、催化剂粉末)、有机化合物(如苯系物、酚类)以及重金属离子(如镍、钒)等。废水的化学需氧量(COD)含量高达 1500 - 3000mg/L,石油类物质浓度在 200 - 500mg/L,pH 值波动范围为 6 - 9,且水量较大,日均产生量约为 500 立方米。
二、絮凝剂选择依据
针对该企业废水特性,经过一系列实验室小试和中试实验,ZUI终选择了一种复合型絮凝剂,其主要成分为聚合氯化铝(PAC)与聚丙烯酰胺(PAM)的复配物。选择的依据如下:
聚合氯化铝(PAC):具有较强的电中和能力,能够快速使废水中带负电荷的胶体颗粒脱稳,形成微小絮体。它对废水中的重金属离子和部分有机物有一定的吸附和络合作用,可以降低 COD 含量。而且,PAC 的水解产物具有较大的比表面积,能为后续 PAM 的絮凝作用提供良好的吸附点位。
聚丙烯酰胺(PAM):作为一种高分子絮凝剂,PAM 可以通过其长链分子的架桥作用,将 PAC 形成的微小絮体进一步连接成较大的絮团,提高絮体的沉降性能和固液分离效果。对于该企业废水中的乳化油和细小悬浮物,PAM 能够有效地促进其絮凝沉淀。同时,PAM 有多种离子类型可供选择,针对该企业废水的弱酸性至弱碱性环境,选用了非离子型 PAM,其适应性更强,絮凝效果更稳定。
三、絮凝剂应用工艺流程
废水预处理:废水首先进入隔油池,通过重力作用去除大部分浮油,浮油回收利用。然后进入调节池,调节废水的水量和水质,使其均匀稳定,同时利用空气搅拌防止悬浮物沉淀。
絮凝反应:
从调节池出来的废水进入絮凝反应池。首先加入 PAC 溶液,通过快速搅拌(搅拌速度约为 150 - 200r/min)使其与废水充分混合,搅拌时间约为 2 - 3 分钟,确保 PAC 均匀分散在废水中并与污染物充分接触,完成电中和与初步絮凝过程。
接着加入 PAM 溶液,PAM 溶液需提前稀释至 0.1% - 0.2% 的浓度,采用慢速搅拌(搅拌速度约为 30 - 50r/min),搅拌时间为 10 - 15 分钟,让 PAM 分子充分发挥架桥作用,形成大而密实的絮体。
沉淀分离:絮凝反应后的废水进入沉淀池,絮体在重力作用下沉淀到池底,上清液通过溢流堰排出进入后续深度处理单元。沉淀池底部的污泥定期排至污泥浓缩池进行后续处理。
四、处理效果评估
石油类物质去除效果:经过絮凝处理后,废水中石油类物质的去除率可达 90% 以上,出口浓度降至 20mg/L 以下,满足当地环保排放标准对石油类物质的排放要求(一般要求低于 30mg/L)。
悬浮物去除效果:悬浮物去除率达到 95% 左右,出水悬浮物浓度低于 50mg/L,使得后续处理单元的负荷大大降低,防止了设备堵塞和管道磨损等问题。
COD 去除效果:COD 去除率约为 60% - 70%,处理后出水 COD 含量在 500 - 800mg/L。虽然不能直接达到排放标准,但为后续的生化处理提供了良好的进水条件,提高了生化处理的效率和稳定性。
五、经济与环境效益分析
经济效益
絮凝剂的使用成本相对较低,每吨废水的絮凝剂费用约为 2 - 3 元。与其他处理方法相比,如膜分离技术等,大大降低了处理成本。
通过对石油类物质和悬浮物的有效去除,减少了后续深度处理设备的维护成本和更换频率。例如,由于进水水质的改善,生化处理系统中的曝气设备、填料等使用寿命延长,减少了设备投资和维修费用。
回收的浮油可以进行再加工利用,产生一定的经济效益,进一步降低了企业的废水处理综合成本。
环境效益
废水处理达标排放,减少了对周边水体环境的污染,保护了当地的生态平衡。石油类物质和有机物的大量去除,降低了水体的富营养化风险,改善了受纳水体的水质状况,有利于水生生物的生存和繁衍。
污泥的妥善处理和处置,避免了二次污染。该企业将污泥进行脱水后,与其他危险废物一并交由有资质的单位进行安全填埋或焚烧处理,符合环保要求,降低了对土壤和大气环境的潜在危害。
综上所述,在该石油化工企业废水处理中,选用的复合型絮凝剂(PAC + PAM)及其应用工艺取得了良好的处理效果,在经济和环境效益方面均有显著表现,为石油化工行业废水处理提供了一个成功的案例参考。
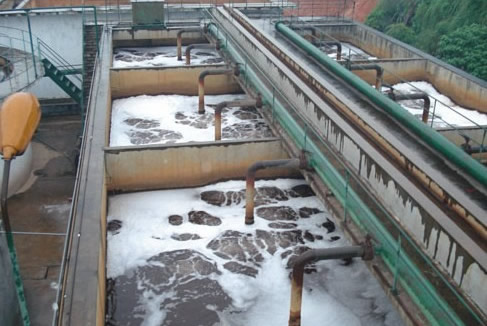